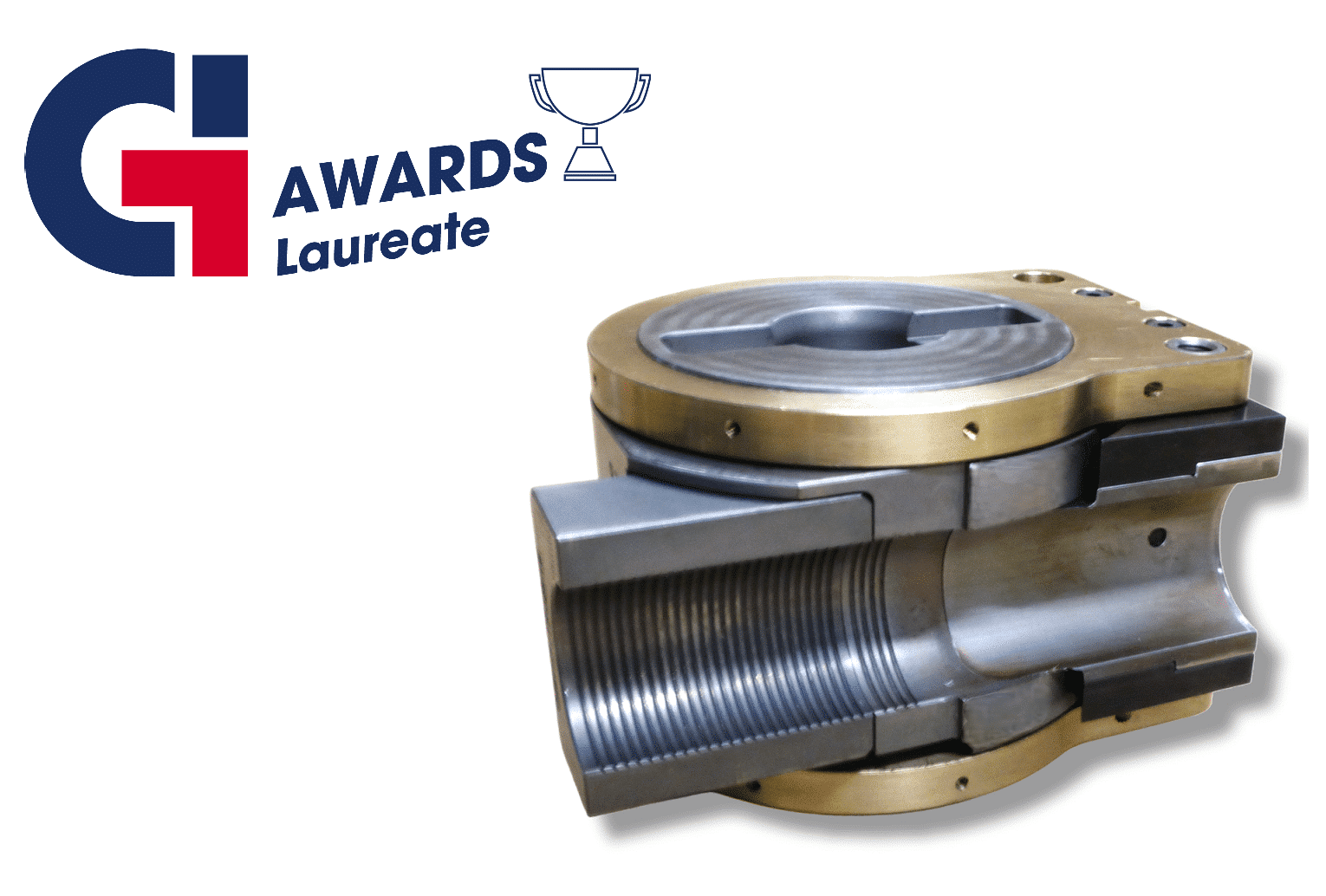
Global Industrie Awards: Bend die with integrated Wiper Die
Specialized in the production of bending tools for more than half a century, Numalliance group posseses numerous patents in the world of tube bending and still keeps innovating! Our latest innovation, focussed at one of the tools necessary for bending, is already changing the world of tube bending… Discover our Integrated Wiper Die. Tube tools for complex tube bending – Rotary Draw Bending Different types of bending components exists (see image on the right) but Numalliance Tube bending machines generally use Rotary Draw Bending. Wiper Die The wiper die is an important part of the bending process, as the final quality of the part depends on this tool. It allows the material on the inside of the bend to be spread out uniformly during the bending operation thus preventing wrinkles. It is a wear part that must be changed regularly. The correct setting of this tool is important for a clean bend and increased wiper die life. Therefore, its installation by experienced operators is a must. All these features combined led to the development of a wiper die bend integrated into the bend die. This innovation has been patented worldwide and has been awarded with the Global Industry Award. Bend die with integrated Wiper Die Set up time eliminated This new tool eliminates the need to set up wiper die postion therefore improving tooling changeover time, repeatibility and part quality. Material and energy savings The design of the integrated wiper die contributes to its rigidity and reduces the wear and tear of the tool considerably. As a result, it greatly increases wiper die life thus reducing its consumption. All these advantages also reduce the quantity of raw material used to produce the wiper die. Consumption of tube is also reduced due to lower rejection as there are less adjustments to do and lower risk of wrong settings. Compatible with automatic tool changeover Fully designed to be integrated into automated cells, this tool can moreover be easily changed with a robot. Its design fully meets the requirements of Industry 4.0. Global Industrie Awards Every year, Global Industry Exhibition organizes GI Awards to highlight innovations that contribute to the improvement of production systems and industrial reconquest. We were nominated in “Production Technology”, one of the 6 categories, and were among 108 other contestants in total this year. We presented and defended our product to a panel composed of industrialists and journalists. Numalliance was presented with its award on March 7th. 2023, during the exhibition, by Niclas Dufourcq, CEO of the BPI. What our customers say… This wiper die was lent to one of our customers for 2 years of production to test and validate its advantages. He described it as a “real success” and a “great move forward”. A project supported by France Relance This project was supported by the French government as part of the France Relance program, designed to encourage innovation and industrial development in France. Want to know more? Download our documentation